Ensuring Safety in Oil and Gas Drilling Operations: Best Practices & Emerging Technologies
Oil and gas drilling is a high-stakes industry that comes with significant safety and environmental risks. However, with the integration of modern drilling technologies and adherence to industry best practices, operations can become safer, more efficient, and environmentally responsible.
This article explores essential safety protocols, cutting-edge technologies, and sustainable practices that support safe and efficient oil and gas drilling operations.
Table of Contents
-
The Importance of Safety in Oil and Gas Drilling Operations
-
Common Hazards in Drilling Environments
-
Technologies That Improve Safety and Efficiency in Oil & Gas Drilling Operations
-
Best Practices for Drilling Operations
-
Environmental Considerations on the Impact of Drilling Operations
-
Environmental Sustainability in Drilling Operations
The Importance of Safety in Oil and Gas Drilling Operations
Drilling operations expose workers to a variety of occupational hazards, including fires, chemical exposure, equipment failure, and extreme weather. Addressing these risks is critical not only for protecting human life but also for maintaining compliance with health and safety regulations.
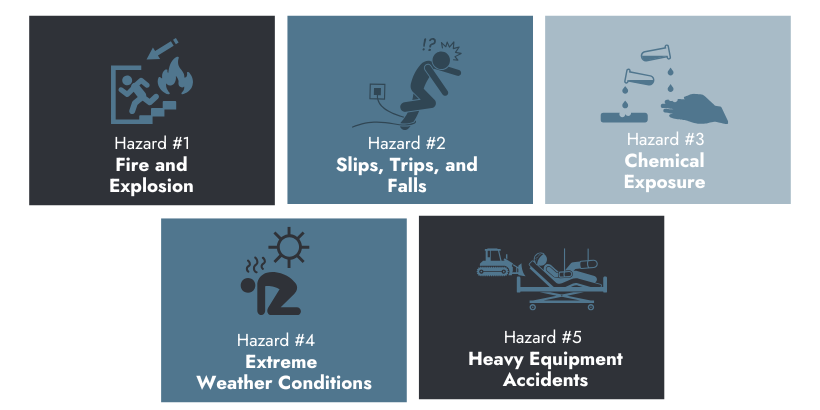
Common Hazards in Drilling Environments
Fire and Explosion Risks
Drilling operations involve the use of machinery, heavy equipment, and flammable chemicals. The combination of these elements presents the risk of fire and explosion if not handled properly. Fire suppression systems and training are critical.
Slips, Trips, and Falls
Oil rigs, especially in wet weather, become hazardous due to slippery surfaces. Well-maintained ladders, stairs, and walkways are critical for injury prevention.
Chemical Exposure
Drilling rigs pose a risk of exposure to harmful chemicals. Workers involved in drilling operations may be exposed to hazardous substances such as benzene, lead, and mercury, which could lead to health problems such as poisoning and cancer. Proper hazard communication, PPE, and air quality monitoring reduce exposure.
Extreme Weather Conditions
Drilling operations can continue even during harsh weather conditions. Workers are at risk of working in extreme temperatures, causing heat or cold stress. Exposure to extreme weather conditions could lead to heat stroke, hypothermia, or other ailments. It is critical to have processes in place to monitor workers' well-being and mitigate the potential impact of severe weather conditions.
Heavy Equipment Accidents
Large, complex machinery introduces risks of mechanical failure and human error. Regular maintenance and operational training help reduce accident rates.
Technologies That Improve Safety and Efficiency in Oil & Gas Drilling Operations
Modern drilling operations increasingly rely on advanced technologies to minimize risk and maximize productivity. These tools allow operators to make data-driven decisions and reduce human exposure to hazardous environments.
1. Advanced Monitoring Systems
Modern monitoring systems have evolved beyond manual checks. These systems now rely on sensors, cameras, and artificial intelligence to provide real-time data on vital parameters such as pressure, temperature, and equipment performance.
For example, some systems use smart sensors to detect pressure fluctuations or gas leaks, enabling crews to respond proactively. These tools also reduce the number of workers required on-site while improving the accuracy of data collection and hazard detection.
2. Well Control Equipment
Well control equipment is critical to preventing blowouts and managing reservoir pressure. These systems include blowout preventers (BOPs), hydraulic controls, and secure panels designed to seal the well during emergencies.
BOPs, often installed on the seafloor or drilling rigs, are engineered to withstand high-pressure, high-temperature (HPHT) conditions. Their ability to shut down a well instantly ensures that energy is contained and the well remains secure when anomalies occur.
3. Automated Drilling Systems
Precision is key in drilling, and automated drilling systems help companies monitor and control the rate, trajectory, and depth of drilling in real-time. These systems leverage advanced software and sensors to provide accurate geological feedback.
By using real-time data, operators can adjust drilling paths, reduce human error, and cut down on non-productive time. The result is improved safety, fewer operational errors, and optimized drilling efficiency.
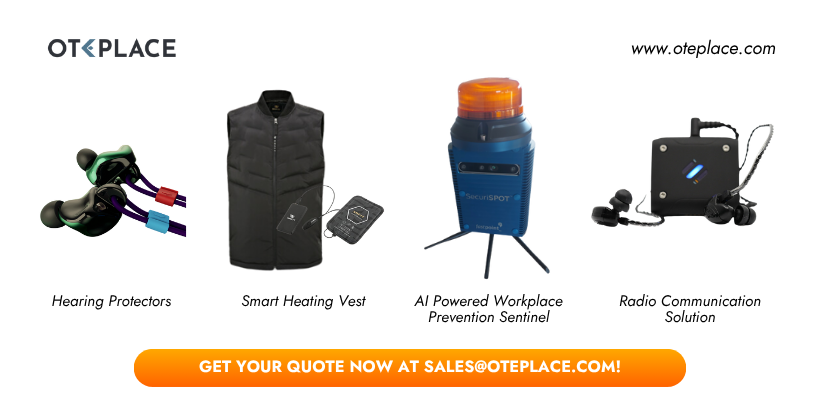
4. Smart Sensors
Smart sensors are compact, portable tools that can be integrated across various drilling components to measure temperature, vibration, pressure, and other key metrics. These sensors transmit real-time data to centralized systems for analysis.
Smart sensors play a crucial role in:Smart sensors play a crucial role in:
-
Detecting early equipment failure
-
Tracking worker exposure to hazardous environments
-
Minimizing downtime and maintenance costs
5. Virtual and Augmented Reality Systems
AR technology can be used to provide real-time information and guidance to operators during drilling operations, reducing the risk of errors and accidents. Virtual and augmented reality systems can also be used to monitor and control drilling equipment and machinery in real time, reducing the risk of accidents, downtime, and waste. For instance, AR glasses can provide operators with a 3D visualization of the wellbore, allowing them to make more informed decisions.
Virtual and augmented reality systems are used in the oil and gas industry to create 3D models of the drilling site, enabling operators to visualize and plan drilling operations with greater accuracy. This technology can also be used in training programs, allowing operators to practice different scenarios and procedures in a virtual environment.
6. Robotics
Robotic systems are revolutionizing safety in oil and gas drilling. These machines perform tasks that are dangerous, repetitive, or physically demanding for humans.
Applications include:
-
Underwater inspections using autonomous underwater vehicles (AUVs)
-
Pipeline maintenance
-
Drill pipe handling and repairs
Equipped with cameras, sensors, and manipulators, robots can function in hazardous or remote environments, reducing the need for human intervention and improving overall site safety.
7. Simulation Software
Simulation software is a computer program that can simulate the behavior and performance of drilling equipment and machinery in various scenarios and conditions. This software can help identify potential problems and areas of improvement, allowing managers to optimize their drilling operations and reduce waste and downtime. This technology can also be used to optimize drilling operations, reducing costs and minimizing the impact on the environment. It can also be used to train workers and simulate emergency situations, enabling them to respond quickly and effectively in case of accidents or equipment failure.
8. Drones
Drones (unmanned aerial vehicles) are increasingly used for:
-
Aerial inspections
-
Site mapping
-
Pipeline surveillance
-
Structural analysis of hard-to-reach locations
Equipped with high-resolution cameras and thermal sensors, drones allow operators to collect data without endangering workers. This helps detect pipeline leaks, structural wear, and potential hazards with precision and speed.
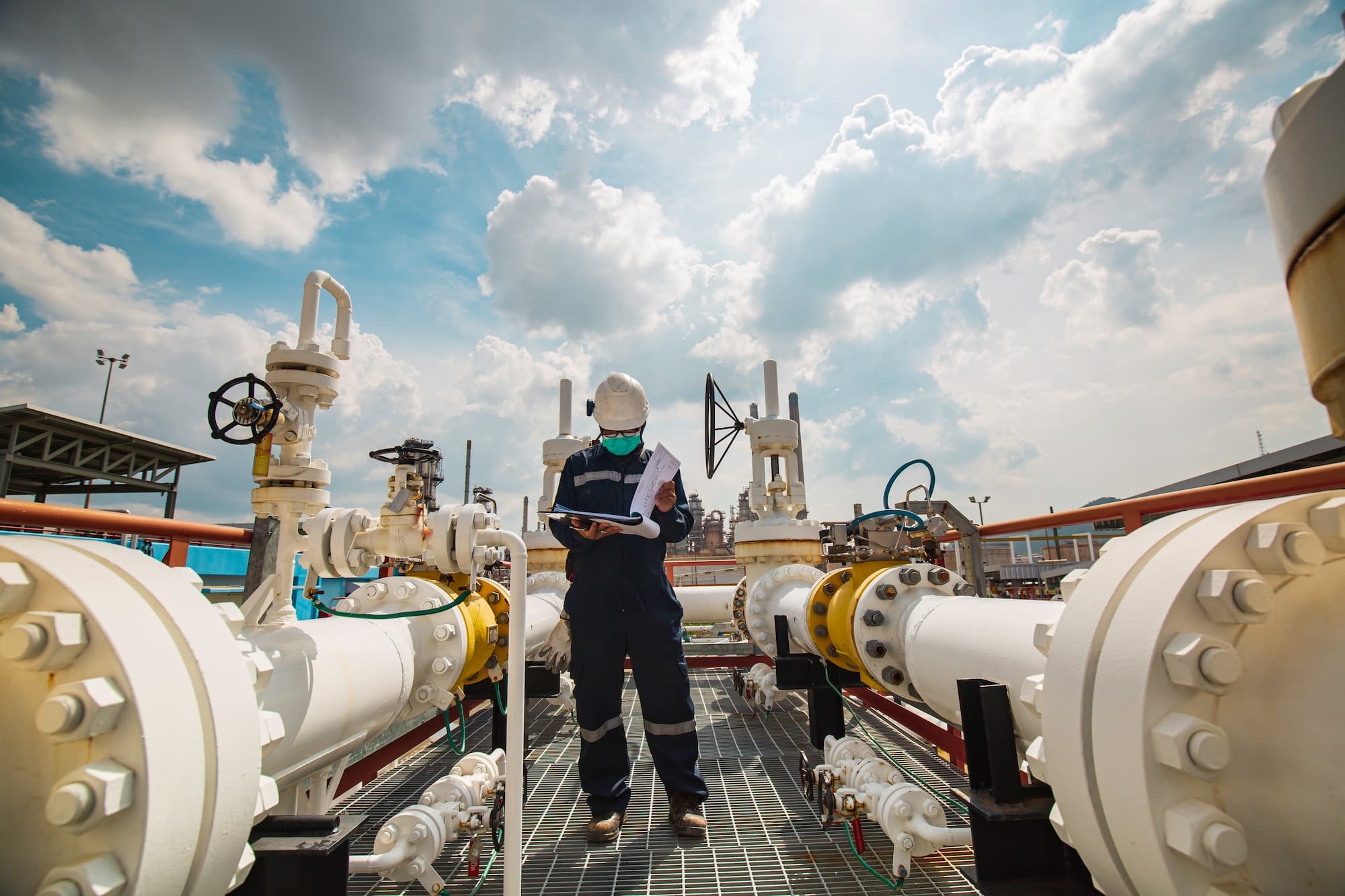
Best Practices for Safe and Efficient Drilling Operations
1. Proper Planning and Preparation
Before drilling, conduct thorough geological surveys and create a wellbore design based on site-specific conditions. A comprehensive drilling plan should cover equipment, fluids, and safety roles.
2. Regular Equipment Maintenance
Downtime from equipment failure is costly. Regular inspections and preventive maintenance programs reduce the chance of mechanical breakdowns and improve worker safety.
3. Effective Communication on Site
Coordination among engineers, rig operators, technicians, and safety staff is essential. Regular safety briefings and hazard reporting protocols foster a safer work environment.
4. Personal Protective Equipment (PPE)
All workers must use approved PPE, such as flame-resistant clothing, gloves, hard hats, and steel-toe boots. Proper use and inspection of gear are critical for injury prevention.
5. Continuous Monitoring and Assessment
Track drilling progress against the plan, conduct routine audits, and evaluate worker compliance with safety protocols. Make adjustments proactively to maintain efficiency and safety.
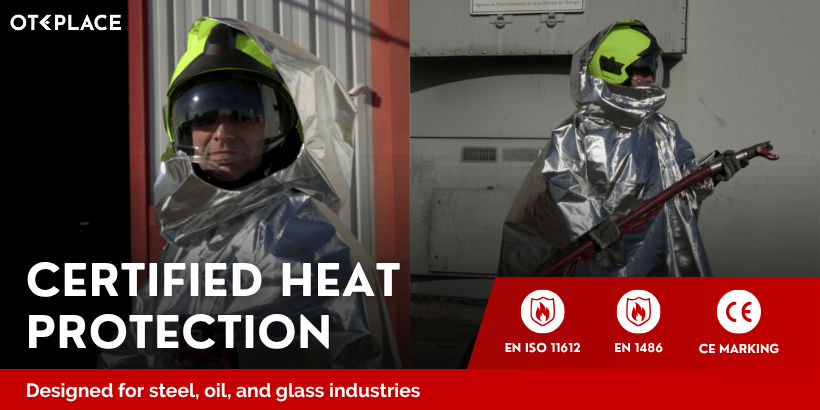
Environmental Considerations in Drilling Operations
The oil and gas industry has a considerable environmental footprint. Addressing environmental risks is crucial to corporate responsibility and regulatory compliance.
Environmental Impact of Drilling
-
Air Pollution: Emissions of VOCs, NOx, and particulates can affect air quality and health.
-
Land Degradation: Spills and soil contamination reduce land fertility and harm ecosystems.
-
Water Contamination: Polluted water sources affect both human health and wildlife.
-
Deforestation: Clearing land for rigs disrupts carbon cycles and natural habitats.
Operators must follow environmental regulations governing waste disposal, emissions, and post-drilling restoration. Non-compliance risks legal action and reputational damage.
Environmental Sustainability in Drilling Operations
To reduce the ecological impact, companies can adopt eco-conscious drilling practices and technologies.
Advanced Drilling Techniques
Horizontal drilling and pad drilling reduce the number of wells needed and limit land disruption. Surface casing helps avoid groundwater contamination.
Effective Waste Management
Implement systems to reduce, reuse, and recycle drilling waste. Responsible disposal practices help prevent environmental contamination.
Use of Renewable Energy
Where possible, incorporate solar or wind power to reduce emissions and reliance on fossil fuel-based electricity.
Green Completion
Capture gas at the wellhead instead of flaring it. This reduces air pollution and conserves resources.
Supporting Safer, Smarter Drilling with Certified Solutions
Achieving safety and efficiency in oil and gas drilling requires more than isolated improvements—it demands an integrated strategy that leverages advanced technologies, rigorous safety protocols, and sustainable practices.
At Oteplace, we understand the high standards of today’s energy sector. That’s why we work with trusted vendors who provide certified safety products and smart solutions that align with the complex needs of modern drilling environments. Whether you're focused on equipment integrity, workforce protection, or environmental compliance, our curated offerings support operations that are both productive and responsible.
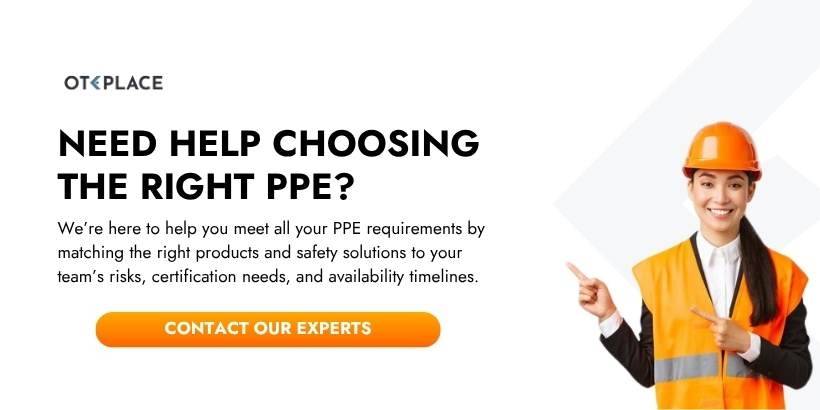