Difference Between a Safety Helmet and a Safety Cap
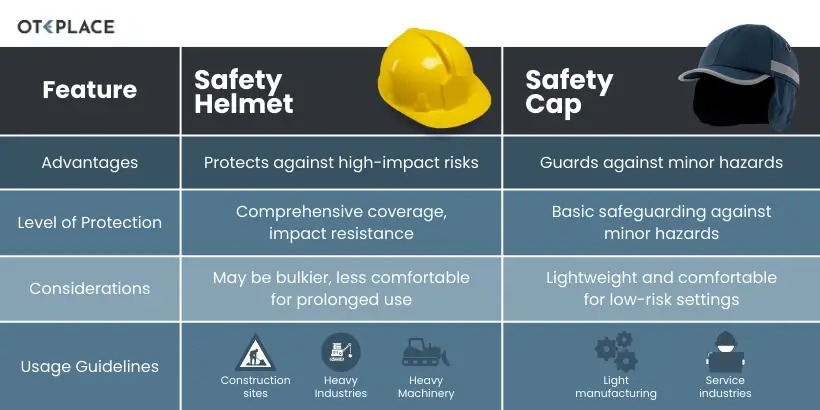
When working in industries like metalworking, foundry, and welding, safeguarding yourself is paramount. Understanding the nuances between safety helmets and safety caps is crucial for optimal protection in these high-risk environments.
What is a Safety Helmet?
Safety helmets are robust protective gear designed explicitly for high-impact scenarios. These helmets are crafted from sturdy materials like fiberglass, thermoplastics, or high-density polyethylene. The construction is engineered to absorb and distribute impact forces, minimizing the risk of head injuries during accidents or collisions.
Unlike safety caps, helmets provide extensive coverage. They encompass the top, sides, and often the back of the head, offering a shield against various angles of impact. Some advanced models may also include additional features like face shields or earmuffs for comprehensive protection.
Safety helmets are essential in environments with significant risks of falling objects, collisions, or impacts. Industries such as construction, heavy manufacturing, welding, and tasks involving heavy machinery mandate the use of safety helmets due to their high-impact resistance and comprehensive coverage.
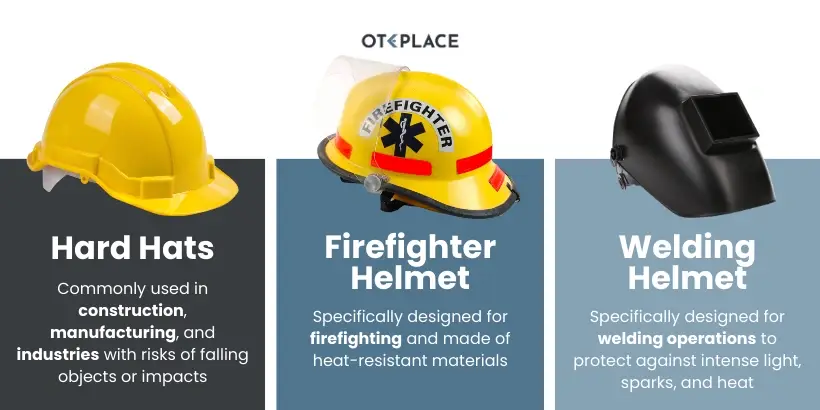
Types of Safety Helmets
- Hard Hats: Standard head protection gear, usually made of durable plastic or fiberglass. Used in construction, manufacturing, and industries with risks of falling objects or impacts. Come with suspension systems to absorb impact energy.
- Firefighter Helmets: Specifically designed for firefighting and made of heat-resistant materials. Protect against high heat and impacts in firefighting and rescue operations.
- Welding Helmets: Equipped with a protective shield, often made of tinted glass or auto-darkening lenses. Specifically designed for welding operations to protect against intense light, sparks, and heat.
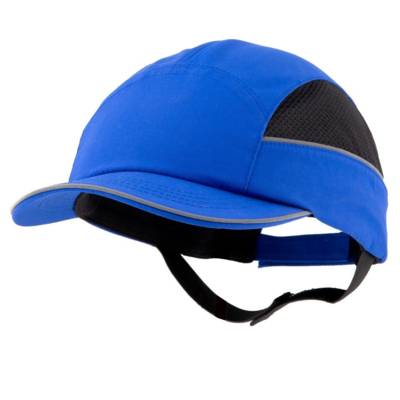
Explore Our Bumpcap Range
What is a Safety Cap?
Safety caps, in contrast, offer more generalized head protection. These caps are designed to guard against minor hazards, such as bumps, low-hanging obstacles, or minor head injuries resulting from minor accidents. They provide a hard outer shell and minimal padding inside, sufficient for deflecting minor impacts.
Resembling caps or hats, safety caps cover the top of the head, providing a lightweight and comfortable option for head protection. They lack the comprehensive coverage and impact resistance found in safety helmets but serve well in environments with lower risk levels.
Safety caps are suitable for environments where the risk of head injury is relatively low or where protection against minor incidents is sufficient. Maintenance tasks, light industrial work, or environments where there's no significant risk of high-impact collisions often adopt safety caps as adequate head protection.
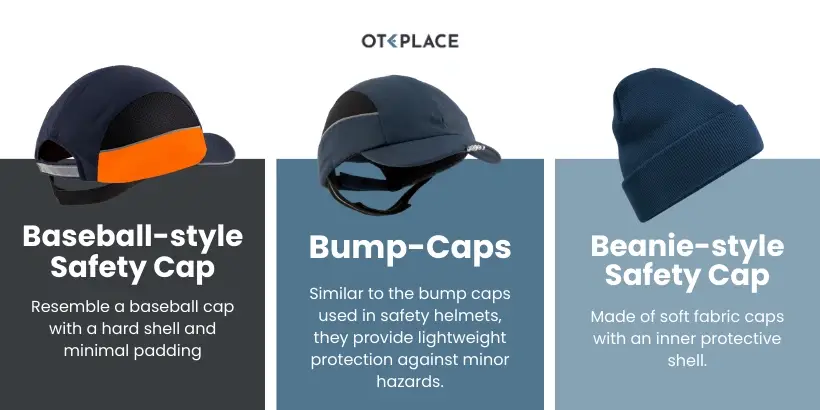
Types of Safety Caps
- Baseball-style Safety Caps:
Resemble a baseball cap with a hard shell and minimal padding. Offer basic protection against minor impacts and bumps. Commonly used in light industrial work or maintenance tasks.
- Bump Caps:
Similar to the bump caps used in safety helmets, they provide lightweight protection against minor hazards. Suitable for environments with low risks, protecting against minor bumps, but lacking the impact resistance of hard hats.
- Beanie-style Safety Caps:
These are made of soft fabric caps with an inner protective shell. These combine comfort with basic protection and are often used in industries where head protection is required without the bulk of traditional hard hats.
Difference Between Safety Helmet and Safety Cap
The primary differences between safety helmets and safety caps lie in their intended use and level of protection. Helmets excel in high-risk environments, offering comprehensive coverage and impact resistance, while safety caps are designed for less intense scenarios, providing basic safeguarding against minor hazards.
The choice between a safety helmet and a safety cap depends entirely on the specific context, the nature of the work, and the level of protection required:
Safety Helmet:
-
Advantages:
Offers comprehensive protection against high-impact risks. Designed to withstand serious accidents or collisions, making it ideal for high-risk environments like construction sites, heavy industries, and tasks involving heavy machinery.
-
Considerations:
Might be bulkier and less comfortable for prolonged use in certain situations. However, modern designs are continuously improving to address comfort without compromising protection.
Safety Cap:
-
Advantages:
Provides basic protection against minor hazards such as bumps, low-hanging obstacles, or minor head injuries. Offers a lightweight and comfortable option suitable for environments where the risk of high-impact collisions is low.
-
Considerations:
Lacks the comprehensive coverage and high-impact resistance of safety helmets. Hence, it may not be adequate in environments with significant risks of serious head injuries.
The choice between an industrial safety cap and a safety helmet depends on the level of risk in the specific work environment. For high-risk environments where serious head injuries are a concern, safety helmets offer superior protection. However, in lower-risk settings where minor hazards are more common, a safety cap might suffice.
In many cases, a combination of both might be used across different tasks within an industry. Employers typically conduct risk assessments to identify the appropriate protective gear needed for different job roles or tasks within their workplace.
Things to Consider When Selecting a Safety Headgear
When choosing between a safety helmet and a safety cap, several critical factors should influence your decision-making process:
Risk Assessment:
Understand the specific hazards in your work environment, considering the nature and severity of potential risks such as falling objects, collisions, impacts, or any other potential head-related injuries.
Level of Protection Required:
Evaluate the level of protection needed based on the identified risks. If the work environment involves high-impact risks or potential serious head injuries, a safety helmet with comprehensive coverage and impact resistance would be more suitable.
Comfort and Fit:
Ensure that the chosen headgear provides a comfortable fit, especially if it needs to be worn for extended periods. Comfort is crucial for user compliance, so the gear should not cause discomfort or restrict movement during work.
Some safety headgears come with ventilation systems, typically in the form of small openings, perforations, or vents strategically placed around them. These vents allow airflow to pass through, helping to improve breathability and reduce heat buildup inside the helmet or cap. Vented headgear is commonly used in industries where workers may need protection while working in hot or humid environments for extended periods.
On the other hand, non-vented safety helmets and caps provide more solid and uninterrupted coverage without openings. These helmets prioritize maximum protection against impacts and falling objects but might be less breathable in comparison to vented designs.
Industry Standards and Regulations:
Check for compliance with industry-specific standards and regulations. Both safety helmets and safety caps should meet or exceed these standards to ensure they offer the necessary level of protection.
Makers of safety helmets and safety caps typically adhere to established standards to ensure their products meet specific safety requirements. These standards are set by various regulatory bodies or organizations globally, depending on the region or industry. Some of the notable standards for safety helmets include:
Safety Helmet Standards:
- ANSI/ISEA Z89.1 (USA): Sets requirements for industrial head protection, including criteria for impact and penetration resistance. It classifies helmets into Type I (top-impact protection) and Type II (top and lateral impact protection).
- EN 397 (Europe): Specifies requirements for industrial safety helmets in terms of impact and penetration resistance, chin strap strength, and other performance criteria.
- AS/NZS 1801 (Australia/New Zealand): Outlines the specifications for industrial protective helmets, covering impact and penetration resistance, construction, and performance requirements.
- CSA Z94.1 (Canada): Canadian standard for protective headwear, covering criteria for impact resistance, penetration, and electrical insulation.
- JIS T 8131 (Japan): Japanese standard for industrial safety helmets, specifying impact resistance, shock absorption, and penetration resistance.
- EN 812 (Europe): Sets standards for industrial bump caps, defining requirements for shock absorption, penetration resistance, and coverage area.
Compliance with these standards ensures that safety helmets and caps meet specific criteria for protection, durability, and performance. Manufacturers often label their products to indicate compliance with these standards, providing assurance to users that the gear meets established safety benchmarks. It's essential for employers and users to verify that the headgear they select adheres to the relevant standards for their industry and region to ensure adequate protection.
Work Environment and Tasks:
Consider the specific tasks and conditions in which the headgear will be used. For instance:
- High-Risk Environments: Workplaces with heavy machinery, construction sites, or industrial settings with a high risk of falling objects or impacts necessitate the use of safety helmets.
- Low-Risk Environments: Warehouse work, maintenance and repair work, site visits to food processing plants involve minimal risk of head injuries from high-impact situations, so safety caps should be enough to protect employees.
Durability and Longevity:
Assess the durability and longevity of the gear. In environments where equipment is subject to frequent use or potential damage, durable headgear ensures sustained protection and longevity.
Cost Consideration:
Evaluate the cost-effectiveness of the gear, considering its quality, durability, and the level of protection it offers. Sometimes, investing more in higher-quality protective gear stock might prove more cost-effective in the long run, especially in high-risk environments.
Flexibility and Adaptability:
Consider whether the headgear is versatile enough to adapt to different work situations within the industry. Some roles or tasks might require varying levels of head protection. Consider also the environment, wherein a cap might be easier to access compared to a helmet.
User Training and Education:
Ensure that employees are adequately trained in the proper use and maintenance of the chosen headgear. Education on the importance of wearing the appropriate gear for specific tasks is crucial for workplace safety.
Employee Feedback:
Gather feedback from ground employees who use the gear regularly. Their insights regarding comfort, practicality, and effectiveness can be valuable when making decisions or adjustments.