Foundry PPE Requirements For Effective Hazard Prevention
In the dynamic and high-risk environment of a foundry, prioritizing the safety of employees is paramount. The stringent requirements for personal protective equipment (PPE) play a crucial role in preventing hazards and ensuring a safe and productive workplace. However, understanding and meeting these requirements can be overwhelming, especially for those new to the industry.
In this comprehensive guide, we delve into the crucial PPE requirements specific to foundries such as glass manufacturing industries and steel mills, providing you with the knowledge and insights necessary to implement effective hazard prevention strategies. From head to toe, we'll break down the essential protective gear and explain why each piece is necessary for specific tasks and potential risks commonly found in foundry environments.
By staying up to date and fully understanding these regulations, you can safeguard your team's well-being, minimize potential accidents, and ensure compliance with industry standards.
Don't compromise on safety—empower yourself with knowledge and take proactive steps towards effective hazard prevention in your foundry.
Table of Contents
-
Importance Of Personal Protective Equipment In Foundries
-
Common Hazards In Foundries And The Need For PPE
-
Understanding The OSHA Regulations For PPE In Foundries
-
Selecting The Right PPE For Different Hazards In Foundries
-
The Role Of Training And Education In PPE Effectiveness
-
Best Practices For Implementing And Enforcing PPE Requirements In Foundries
-
Evaluating The Effectiveness Of PPE Programs In Foundries
-
Final Thoughts On Effective Prevention Of Hazards Through Foundry PPE
-
Frequently Asked Questions - FAQ
Importance Of Personal Protective Equipment In Foundries
Foundries are inherently hazardous environments, with workers exposed to chemical hazards, extreme temperatures, and physical dangers. In such settings, PPE is essential for safeguarding employees and minimizing potential injuries.
PPE acts as a barrier between workers and the hazards they face daily, providing crucial protection for the head, face, eyes, ears, respiratory system, hands, and feet. To understand the importance of PPE in foundries, let's delve deeper into the common hazards these environments present and the corresponding PPE requirements.
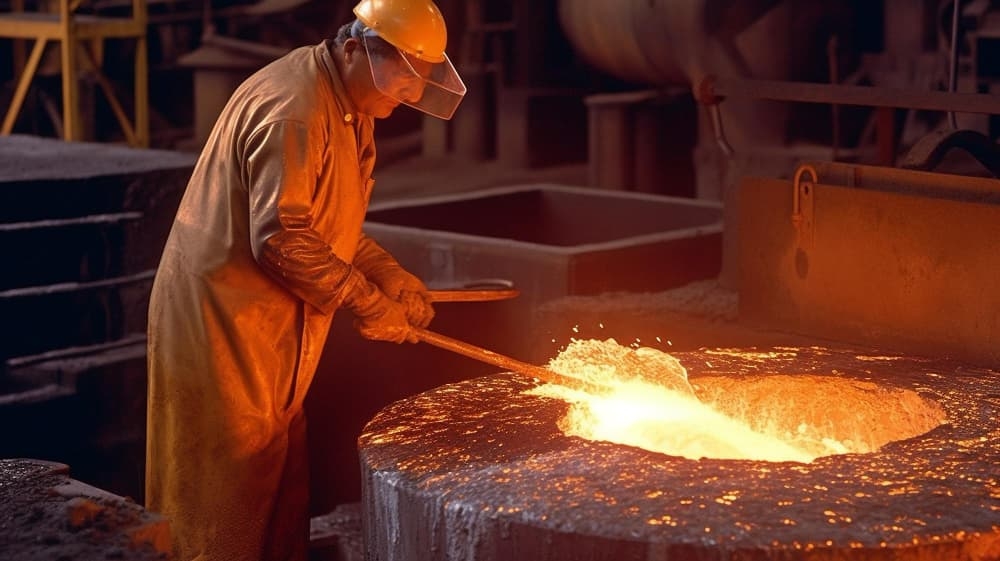
Common Hazards In Foundries And The Need For PPE
Foundries are known for their intense heat and exposure to molten metals, making burns a significant risk. Additionally, the handling of chemicals, such as binders and solvents, poses health hazards, including respiratory issues and skin irritation.
The melting process in foundries involves extremely high temperatures, often exceeding 1000 degrees Celsius. Workers who come into contact with molten metal splash or work in radiant heat are at risk of burns and heat stress. Physical hazards, such as falling objects and machinery accidents, are also prevalent.
To effectively protect against these hazards, specific PPE requirements must be met. Let's explore the Occupational Safety and Health Administration (OSHA) regulations for PPE in foundries to gain a better understanding of the necessary protective gear.
Understanding The OSHA Regulations For PPE In Foundries
OSHA sets the guidelines and standards for workplace safety in the United States. For foundries, OSHA's regulations provide clear directives on the use of PPE to ensure the well-being of employees. These regulations outline the specific types of PPE required for various tasks and hazards encountered in foundries.
One of the most crucial pieces of PPE in foundries is protective clothing. OSHA mandates that employees working in areas where they may be exposed to molten metal or other hazardous substances wear molten metal protective clothing made of materials such as leather or aluminized fabric.
This protective clothing should cover the entire body, including the arms, legs, and torso, to minimize the risk of molten metal splash hazards, contact with radiant heat, or other injuries. Make sure that it does not trap molten metal in pockets or any loose legging tops.
Another essential form of PPE in foundries is eye and face protection. OSHA requires employers to provide employees with appropriate goggles or face shields to shield against flying objects, sparks, and splashes. These protective devices should be made of materials that can withstand impact and heat, ensuring that workers' eyes and faces remain safe from harm.
Respiratory protection is also a critical aspect of PPE in foundries. The processes involved in foundry work often generate dust, welding fumes, and other flying particles that can be harmful if inhaled. OSHA regulations stipulate that employers must provide employees with respirators when necessary to protect against these hazards. The type of respirator required depends on the specific contaminants present and their concentration levels.
Dust Masks (Filtering Facepiece Respirators, FFRs):
These are disposable respirators that provide protection against non-toxic dust and particulates. They are typically rated with an N, R, or P designation followed by a number (e.g., N95), which indicates their level of filtration efficiency. N95 masks, for example, are commonly used in metalworking to protect against airborne particulates.
Half-Face Respirators:
These respirators cover the nose and mouth and use replaceable filter cartridges to protect against various hazards, such as dust, fumes, and organic vapors. They provide a better seal than dust masks and can accommodate different filter types depending on the specific hazard.
Full-Face Respirators:
These respirators cover the entire face and provide protection for the eyes as well. They are suitable for environments with more severe exposure to gasses, fumes, or chemicals. The use of full-face respirators is common when dealing with hazardous gasses in foundries and metalworking.
Powered Air-Purifying Respirators (PAPRs):
PAPRs use a battery-powered blower to force air through filters, providing a continuous supply of clean air to the user. They are more comfortable to wear for extended periods and offer a higher level of protection against particulates and gasses. PAPRs are often used in foundries and metalworking for enhanced protection.
Supplied Air Respirators (SARs):
SARs deliver clean air from an external source (e.g., an air compressor or tank) to the user via a hose and facepiece. This type of respirator is used when there is a risk of exposure to extremely toxic gasses or low-oxygen environments, as it ensures a constant supply of breathable air.
Selecting The Right PPE For Different Hazards In Foundries
Choosing the appropriate PPE for specific hazards in foundries is crucial for providing effective protection. Consider the nature of the tasks performed and the potential risks associated with them.
For head protection, hard hats with a suspension system should be selected to absorb impact and distribute force in the event of falling objects. Ensure that the hard hat fits properly and is regularly inspected for damage.
When it comes to eye and face protection, safety glasses with side shields are suitable for general protection against impact and airborne particles. However, in situations where there is a risk of molten metal splashes or chemical exposure, face shields or goggles should be used. These provide additional coverage and protect the face from direct contact with hazardous materials.
Respiratory protective equipment should be selected based on the specific airborne hazards present in the foundry. Respirators with appropriate filters or cartridges should be used to prevent the inhalation of harmful fumes, dust, or gasses. It's crucial to ensure that respirators fit properly and are regularly maintained and replaced as needed.
When it comes to hand protection, heat or flame-resistant gloves are essential for foundry workers. These protective gloves should be made from materials that can withstand high temperatures, such as leather or aluminized fabric. Gauntlets can provide additional forearm protection, especially when pouring molten metal. Regular inspection and replacement of gloves are necessary to ensure their effectiveness.
Protecting the feet in foundries requires heat or flame-resistant boots with toe protection. These boots should have appropriate insulation to guard against extreme temperatures and provide additional support to prevent slips and falls. Metatarsal guards can be used to protect the upper foot area from heavy objects.
By selecting the right PPE for different hazards, foundries can significantly reduce the risk of injuries and ensure the safety of their employees.
Here are some of the standards to consider when selecting a foundry PPE:
- ISO 15025:2016: This outlines two methods, namely surface ignition and bottom-edge ignition, used to assess the flame spread characteristics of vertically positioned flexible materials. These materials can be single or multicomponent fabrics, which encompass coated, quilted, multilayered, sandwich constructions, and comparable combinations. This evaluation is conducted under controlled conditions involving exposure to a small, predefined flame source.
- ISO 9151:2016: ISO 9151:2016 outlines a procedure for assessing the heat transmission characteristics of materials or material assemblies employed in protective clothing. The method involves ranking materials by comparing heat transfer indices, which offer insight into the relative heat transfer performance under the specific testing conditions.
- ISO 6942:2002: ISO 6942 outlines two complementary methods, denoted as method A and method B, designed to evaluate the performance of materials used in heat protective clothing when exposed to heat radiation.
- ISO 9185:2007: ISO 9185:2007 delineates a method for evaluating the resistance of materials, meant for use in protective clothing against large splashes of molten metal, to the penetration of heat. The standard furnishes precise procedures for assessing the consequences of molten metal splashes, including molten aluminum, molten cryolite, molten copper, molten iron, and molten mild steel.
- ISO 12127-1:2015: ISO 12127-1:2015 outlines a test method used to ascertain contact heat transmission. This method applies to both protective clothing, including hand protectors, and the materials used to create them. Its purpose is to assess the ability of these materials to safeguard against elevated contact temperatures.
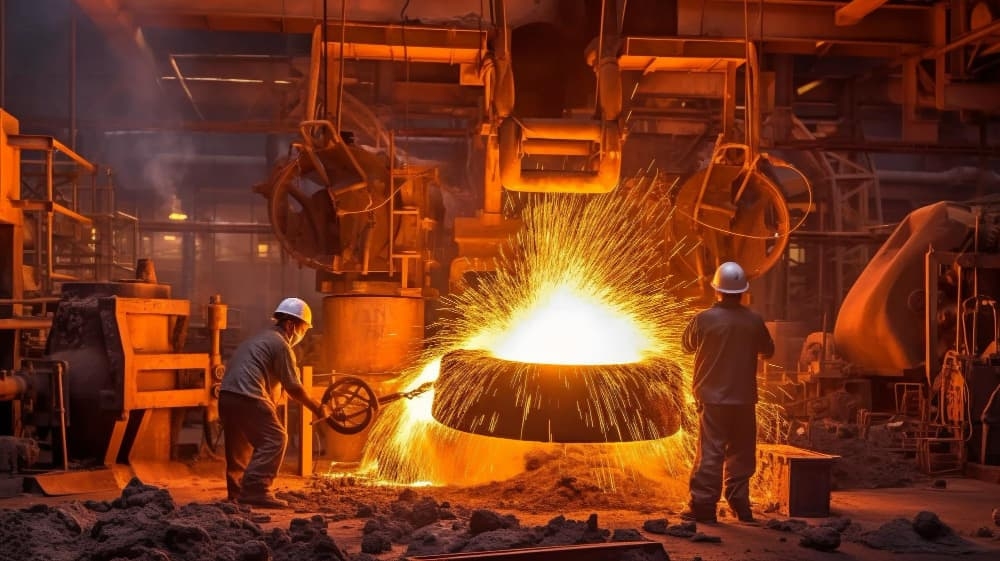
The Role Of Training And Education In PPE Effectiveness
Having the right PPE is only part of the equation. Proper training and education on the correct use, maintenance, and limitations of PPE are essential for its effectiveness.
Employees must receive thorough training on the proper donning and doffing of PPE. They should understand how to inspect PPE for damage or wear and know when to replace it. Training should also cover the limitations of PPE, emphasizing the importance of using engineering controls and safe work practices in conjunction with PPE.
Supervisors and managers play a crucial role in ensuring compliance with PPE requirements. They should lead by example, consistently wearing and enforcing the use of PPE. Regular communication and reinforcement of PPE policies and procedures are vital to maintaining a culture of safety.
Best Practices For Implementing And Enforcing PPE Requirements In Foundries
Implementing and enforcing PPE requirements in foundries requires a systematic approach. Here are a few practices you can start implementing after careful consideration.
Identify and assess the specific hazards present in your foundry to determine the appropriate PPE requirements.
Engage employees in the decision-making process when selecting PPE. Their input can provide valuable insights and increase compliance.
Ensure that all employees receive thorough training on PPE use, maintenance, and limitations. Regular refresher courses and updates on industry best practices are essential.
Develop and communicate clear policies and procedures regarding PPE requirements. Make it a part of the company's safety culture.
Implement a regular inspection and maintenance program for PPE. Replace damaged or worn-out equipment promptly.
Create an environment where employees feel comfortable reporting PPE-related issues or suggesting improvements. Ensure regular reviewing of feedback and make adjustments accordingly.
By following these best practices, foundries can ensure the effective implementation and enforcement of PPE requirements, fostering a safe work environment for all employees.
Evaluating The Effectiveness Of PPE Programs In Foundries
Regular evaluation of PPE programs is essential to identify areas for improvement and ensure ongoing effectiveness. Here are some key factors to consider when evaluating the effectiveness of PPE programs in foundries:
- Compliance
Assess the level of PPE compliance among employees. Regular observations and audits can help identify any non-compliance issues and areas for improvement. - Incident Rates
Analyze the incident rates and types of injuries or accidents occurring in the foundry. Evaluate whether PPE played a role in preventing or minimizing these incidents. - Employee Feedback
Solicit feedback from employees regarding the comfort, fit, and effectiveness of the PPE provided. Respond promptly to suggestions and concerns regarding improvement. - Training Effectiveness
Evaluate the effectiveness of PPE training programs through assessments and surveys. Identify any gaps in knowledge or areas requiring additional training. - Maintenance And Inspection
Review the maintenance and inspection records of PPE to ensure that equipment is regularly checked and replaced as needed.
By regularly evaluating PPE programs, foundries can make data-driven decisions to improve safety and protect their employees.
Final Thoughts On Effective Prevention Of Hazards Through Foundry PPE
In the dynamic and high-risk environment of a foundry, prioritizing the safety of employees is paramount. Understanding and meeting the crucial PPE requirements specific to foundries is essential for effective hazard prevention.
By following the regulations set by organizations like OSHA, selecting the right PPE for different hazards, providing proper training and education, and implementing best practices, foundries can create a safe and compliant workplace. Regular evaluation of PPE programs and considering the cost-benefit analysis of investing in PPE further enhance safety and productivity.
Don't compromise on safety—empower yourself with knowledge and take proactive steps towards effective hazard prevention in your foundry. By prioritizing the well-being of your team and ensuring compliance with PPE requirements, you can create a safer and more productive work environment.
Need Help?Frequently Asked Questions - FAQ
Why is PPE required in foundry?
PPE is required in a foundry due to the constant exposure of workers to various hazards. It safeguards employees and minimizes the risk of injuries from molten metals and other dangers.
What are OSHA regulations for PPE in foundry?
OSHA regulations for PPE in foundry require workers to wear protective clothing made of materials like leather or aluminized fabric, as well as respirators, eye protection, and face protection to protect against hazards like molten metals.
Why is training and educating effective in PPE?
Training and education in PPE are effective in a foundry environment as they ensure that workers understand the importance of protective measures, helping to prevent accidents and injuries.
How to implement and enforce PPE in foundry?
To implement and enforce PPE in a foundry, it is necessary to identify and assess specific hazards, provide employee training, develop clear policies and procedures, and more, to ensure the safety of workers.
What to consider when evaluating PPE in foundry?
When evaluating PPE in a foundry, consider factors such as compliance with regulations, incident rates, employee feedback, the effectiveness of training, and proper maintenance of protective equipment.
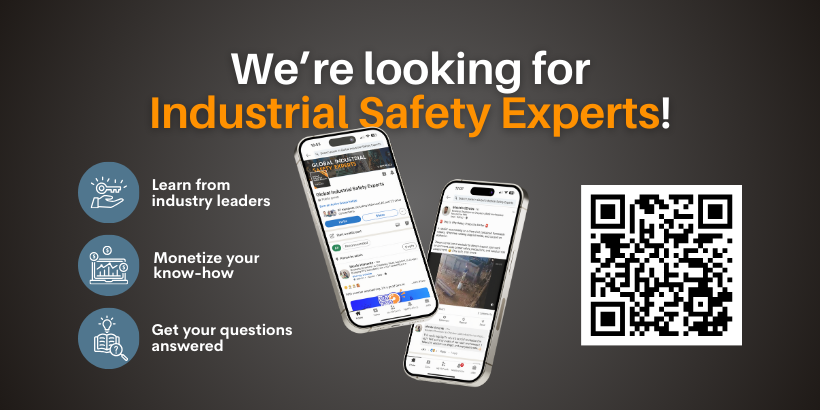