Top 6 Machinery And Heavy Equipment Safety Tips To Consider
Heavy equipment and machinery are essential tools in various industries, including construction, manufacturing, mining, and agriculture. Though these machines simplify the work of operators, they also pose numerous dangers.
People who work with or around heavy machinery and equipment know that safety is always a top priority. Accidents can happen in no time, and the risks are high. Whether you are new to the job or have been doing this for a while, it never hurts to review safety guidelines and procedures.
Accidents involving heavy machinery can cause severe injury or fatality. To prevent such outcomes, we've compiled six essential machinery and heavy equipment safety tips. Following these practices will increase your safety, as well as those around you.
The Need For Heavy Construction Equipment and Equipment Safety
The construction industry requires specialized operating equipment and skills. Many tasks performed on the construction site require heavy machineries such as bulldozers, cranes, and excavators. Construction work involves a high level of risk, and without proper equipment or safety measures, workers may face serious injuries, disability, or even death.
Here we will discuss the need for heavy construction equipment and why equipment safety is of utmost importance.
Ensuring Heavy Equipment Safety
-
Increased Efficiency
Heavy construction equipment like cranes, bulldozers, and excavators are designed to perform complex tasks that humans cannot perform, like moving huge boulders or excavating soil from the foundation of a building. These machines are equipped with advanced technology that enables operators to complete tasks quickly and efficiently, a task that would have taken a team of workers days or even weeks to accomplish.
This increased efficiency of construction work means projects can be completed on schedule, saving companies time and money, and also boosting the economy.
-
Improved Safety
Safety is critical on construction sites, and without proper equipment or safety measures, workers are exposed to some hazardous and life-threatening situations. Heavy machines are designed with several safety features that prevent accidents from occurring, such as backup alarms, cameras, motion sensors, and rollover protection.
Additionally, construction companies must ensure every heavy equipment operator receives proper training and certification to operate heavy equipment safely.
-
Reduced Labor Costs
Using heavy equipment allows construction companies to accomplish more work in less time, reducing the need for larger teams of manual laborers. This means reduced labor costs for companies, which can translate to labor-saving advantages, such as better work quality, faster completion times, and increased profits.
Additionally, heavy equipment operation means that labor-related injuries and accidents can generally decrease, as fewer people are required to perform many tasks.
-
Improved Accuracy and Quality
Traditional methods of construction work can lack accuracy and precision. Heavy construction equipment is manufactured with advanced technology that ensures work is done with perfect accuracy and quality.
Precision in construction work is crucial, as it ensures that buildings and structures are structurally sound and up to standards, improving the quality of the building and reducing the occurrence of structural failures.
The Role Of Training In Heavy Equipment Operation
Operating heavy machinery and equipment is not an easy feat, and it's certainly not one that should be taken lightly. The role of heavy equipment operators is critical in ensuring the efficient execution of a wide range of industrial and construction projects. That's why it is essential to ensure that heavy equipment operators are well-trained and equipped with the necessary skills to operate construction machinery safely and efficiently.
Here are some of the reasons why training is critical:
Safety
A key reason why training is so important is safety. Operating heavy equipment requires skills that are not easy to acquire, and if a person does not have the necessary skills and experience, the risk of workplace accidents increases.
Safety training is the first step in ensuring that workers are aware of the hazards involved in operating heavy equipment, and it shows them how they can protect themselves and their coworkers from harm. This type of training is beneficial to all employees in a company, and it can prevent accidents before they happen.
Efficiency
Efficiency is another significant benefit of training. When operators are trained, they understand how to operate the equipment correctly, so they don't waste time or make mistakes. This results in a more efficient job site and an overall better bottom line.
Additionally, those who are well-trained in heavy equipment operation are more effective at identifying issues and troubleshooting, resulting in a more streamlined operation from start to finish.
Regulatory Compliance
In many instances, proper training is required to meet regulatory compliance standards. This is because governments and regulatory agencies believe safety should be a top priority, and they want to ensure that employers and employees understand the risks involved in heavy equipment operations.
By training everyone properly, companies can demonstrate their commitment to safety, which can also save them money by preventing fines and penalties.
Ensuring Heavy Equipment Safety Via Regular Inspection And Maintenance Drives
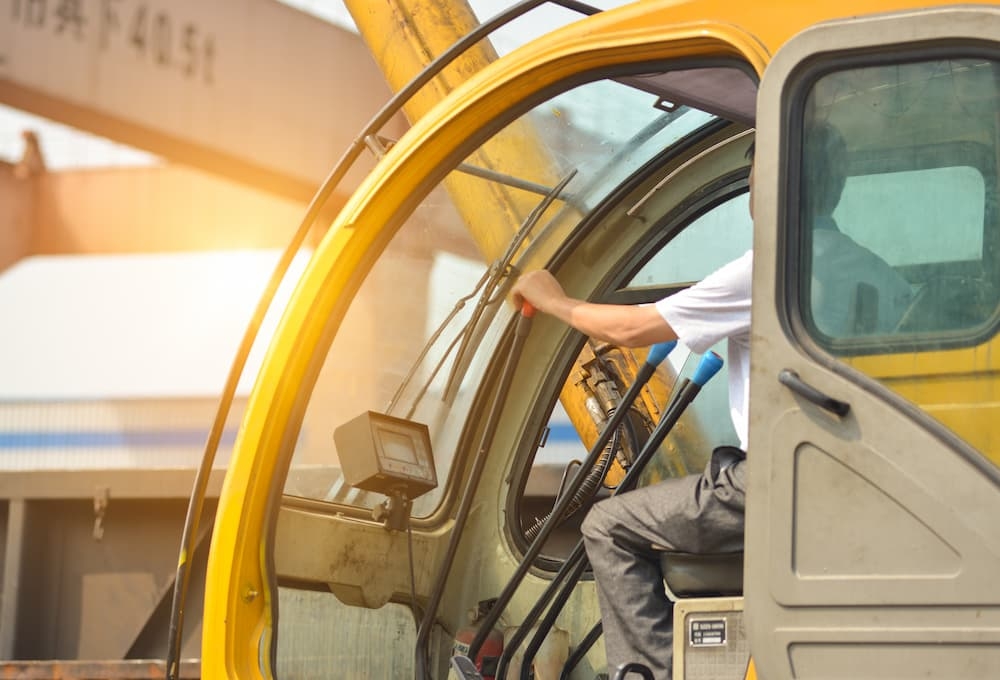
As a heavy equipment operator, you know how important your equipment is to your daily work. But do you know how essential regular inspection and maintenance are to ensure your equipment is safe to use?
Many operators may overlook the importance of routine maintenance, but it's critical not only for the lifespan of the machinery but also for the safety of the operator and those nearby.
First and foremost, regular inspections and maintenance are necessary to ensure the safety of the operator and all persons onsite. Heavy equipment, such as cranes, bulldozers, and excavators, can weigh several tons and require proper maintenance and inspection to operate safely.
Without regular maintenance, the equipment can malfunction, causing accidents on the job site. Failing to maintain equipment is negligent and could lead to severe consequences. Therefore, it is crucial to have a regular inspection and maintenance schedule to keep everything running safely.
Furthermore, when operators fail to maintain their heavy equipment, they risk reducing its lifespan. With regular maintenance, the equipment can function optimally, and when something is not working correctly, it can be immediately addressed, which can prevent further damage.
Regular maintenance also helps operators and companies avoid downtime, maintain productivity, and reduce unwanted costs due to delays. Heavy equipment should not only be regularly tested and inspected but diligent records should also be kept. Failing to comply can result in hefty fines and legal fees.
Heavy Equipment Safety And Hazard Identification
Heavy equipment operators are vital to the construction, mining, and transportation industries, to name a few. However, working with heavy equipment can be dangerous, and it’s essential to identify and prevent hazards to keep yourself and others safe. Here are some common hazards associated with heavy equipment operations and how to mitigate them.
Mechanical Hazards
Heavy equipment and machinery are often powered by hydraulic or electrical systems. The mechanical parts in these systems can be hazardous if they malfunction or are not adequately maintained.
Examples include worn or damaged parts that can lead to equipment failure, loose or detached parts that can cause entanglement or lacerations, and metal shards that can fly off and injure employees. Checking for signs of wear, performing routine inspections and maintenance, and using safety guards, especially in blind spots, can help prevent mechanical hazards. Additional personal protective equipment (PPE) and accessories may include but are not limited to:
Protective gloves: Butyl rubber gloves, nitrile gloves, etc.
- Safety goggles or face shields
- Steel-toed boots or safety shoes
- High-visibility vests or clothing
Crush Hazards
Heavy equipment and machinery are large and powerful, and they can inflict severe injuries through crushing or pinning. Examples include tipping and overturning, collision with other objects or equipment, and getting caught in-between components and moving vehicle parts.
Such accidents can be fatal, and it’s essential to prevent them by wearing a simple seat belt or harness, avoiding overloading or overbalancing the equipment, keeping a safe distance from other vehicles and equipment, and implementing traffic control measures. Additional PPE and accessories may include:
Personal fall protection equipment, such as harnesses and lanyards
Hard hats
Safety boots or shoes with reinforced toes and metatarsal guards
High-visibility clothing with reflective tape
Noise Hazards
Heavy equipment and machinery are large and powerful, and they can inflict severe injuries through crushing or pinning. Examples include tipping and overturning, collision with other objects or equipment, and getting caught in-between components and moving vehicle parts.
Foam earplugs
Silicone earplugs
Flanged earplugs
Earmuffs with noise reduction rating (NRR) specifications
Employers can also implement noise control measures, such as enclosing the equipment, using noise-absorbing materials, or scheduling noisy operations during less busy times.
Chemical Hazards
Heavy equipment operators may be exposed to harmful chemicals, such as fuels, oils, lubricants, and solvents, during maintenance or refueling. Prolonged or repeated exposure can lead to respiratory problems, skin irritations or burns, and other health issues.
Adhering to proper procedures, using the appropriate PPE (e.g., gloves like butyl rubber gloves, nitrile gloves, goggles, respirators), and ensuring proper ventilation can help prevent chemical hazards. Additional accessories may include:
Chemical-resistant aprons
Protective suits or coveralls
Chemical-resistant boots
Chemical-resistant face shields or goggles
Respiratory protection with specific filters for chemical vapors
By using these additional examples of specific PPE, EPC, and accessories, operators can enhance their safety measures and mitigate the risks associated with heavy equipment operations.
-
The Need For Suitable PPE
Working with heavy equipment can lead to various kinds of injuries, including head injuries, spinal damage, fractures, and hearing problems. Not to mention, machines can emit hazardous elements such as chemicals and metal particles that can cause respiratory illness, skin irritation, or burns.
Therefore, PPE serves as a protection mechanism against potential danger, and it's essential to adhere to equipment-specific recommendations before starting work. Besides, some companies and organizations have strict PPE policies that workers must follow.
There are several PPE options depending on the kind of job and available tools. Here are a few of the most common PPEs used in heavy equipment operations.
-
Hard Hats
Essential when working in construction sites that require employees to be around cranes or other objects that might fall on their heads
-
Eye and Face Protection
Depending on the job, a full-face shield or goggles are essential when working with heavy equipment that may emit particles, fumes, or dust that can damage eyes and cause respiratory illnesses
Respiratory Protection
Jobs that involve working with hazardous chemicals, dust, or mold require a protective mask or respirator.
Protective Clothing
Wearing protective clothing such as gloves, steel-toed boots, and reflective vests can protect hands and feet from injury and keep workers visible in low-light conditions.
Choosing The Appropriate PPE
It's essential to select the right PPE for the job site. The choice of PPE depends on the type of hazard present in the workplace. For example, safety glasses and face shields are necessary when working with welding equipment to protect the eyes and face from bright sparks and fumes.
Respiratory equipment like respirators, dust masks, and air-supplied helmets should be worn when working in dusty environments, spray painting, and in other activities with harmful chemicals. Additionally, safety footwear, gloves, and hard hats should be a mandatory set of PPE for every heavy equipment operator.